2020-08-24
Lightweight solution for thin-walled die-cast part
RINGSPANN clamping fixtures enable precision machining across several process stages
Whenever rotationally symmetrical die-cast components with thin walls have to be machined in the production of modern automotive transmissions, the demands on the clamping technology increase considerably. This is because the clamping systems used for this purpose must exhibit a high degree of concentricity, must not deform the workpiece under any circumstances and should ensure optimum chip removal. RINGSPANN has therefore developed a clamping trio specifically for external and internal machining as well as for the balancing and crack detection of sensitive aluminium gear pots, which has quickly established itself as a semi-standard in large series production.
Bad Homburg, August 2020. – Even clamping systems can have a career. An extremely vivid example of this are the three clamping systems that RINGSPANN has recently realised for the production of lightweight components for modern 8HP generation automatic car transmissions. Within the space of just a few months, this innovative triple clamping fixture for external and internal machining, as well as for the balancing and crack detection of die-cast aluminium transmission pots, has become a permanent fixture in a large number of large series production lines. "Today, it is used not only in Germany but also overseas," reports Volker Schlautmann, head of RINGSPANN’s clamping fixtures/ shaft-hub-connections customer team.
Also suitable for small machines
The design and functionality of these clamping fixtures are optimally tailored to the high quality and efficiency demands in gear manufacturing. Above all, this means: They ensure that the thin-walled aluminium components are held with as little distortion as possible, they meet the high demands on precision and concentricity in all machining process stages, and they support reliable chip removal during turning (inside and outside). In addition, all three clamping devices convince with what is principally a rather simple design and a low dead weight. Volker Schlautmann is therefore keen to stress: "After minimal training by our team, the user is quickly able to perform the maintenance themselves, and thanks to their lightweight construction, our clamping devices can also easily be used on smaller processing machines with lower spindle loads". The RINGSPANN trio thus directly contributes towards both reducing the total investment for a production line and lowering unit costs.
Secure and low-distortion clamping
The two clamping fixtures for machining the cast aluminium blanks are, on the one hand, a pneumatically and mechanically actuated double diaphragm mandrel (external turning) and, on the other hand, a pneumatically and mechanically operated flat chuck-clamping chuck combination (internal turning). The clamping fixture for the two subsequent process steps of balancing and crack detection, on the other hand, is a mechanically operated double taper collect clamping mandrel. What all three systems have in common is that they clamp the cylindrical workpiece at the upper and lower edge - i.e. at both ends. The frictional connection is achieved with two independently acting, circularly arranged clamping elements. They ensure that the gear pot, whose wall thickness is reduced from a little more than 4.0 mm to just 2.2 mm during turning, always rests securely and - above all - with minimal distortion in the clamping. Additional vibration dampers also prevent the rotating gear pot from vibrating during the machining of its surfaces, which are interrupted by numerous holes. In combination with the open design of RINGSPANN’s clamping systems, these bores facilitate the smooth removal of the fine aluminium chips.
Designed for long service life
All three RINGSPANN clamping systems for the machining and quality assurance of die-cast aluminium gear pots have a concentricity accuracy of ≤ 40 µm and are designed for very long tool life. They are currently proving their worth in several large series projects with batch sizes in the multi-million range and are being used in both European and US production lines. Their customer-oriented and product-specific design and configuration once again underlines the high level of competence of RINGSPANN engineers in the field of clamping systems for use in the large-scale production of gear manufacturing, fluid power and gearing technology. "Whenever round, cylindrical and rotationally symmetrical workpieces need to be machined with minimum tolerances, our clamping technology expertise is the right choice. Thanks to our more than 75 years of experience in this field, we are able to create high-quality clamping systems that reliably fulfil their task over a long period of time, even for completely new clamping situations or special conditions - such as in the case of the thin-walled die-cast parts described above. And if our wide range of standard precision clamping fixtures should not cover the task at hand, we set ourselves the goal of developing a new standard clamping fixture based on a special solution," says RINGSPANN expert Volker Schlautmann. ms
Innovative clamping technology for the machining of thin-walled gear pots
- Lightweight construction
- Two clamping points, pneumatically and mechanically operated
- Clamping with draw-down effect
- Air system control in three contact bolts
- Spring-actuated vibration dampers, they contact the contour of the workpiece during rotation
- Lightweight construction
- Two clamping points, pneumatically and mechanically operated
- Clamping with draw-down effect
- Air system control in three contact bolts
- Open design optimises chip removal
- Lightweight construction
- Two clamping points; mechanically actuated via two spring packs
- Clamping with draw-down effect
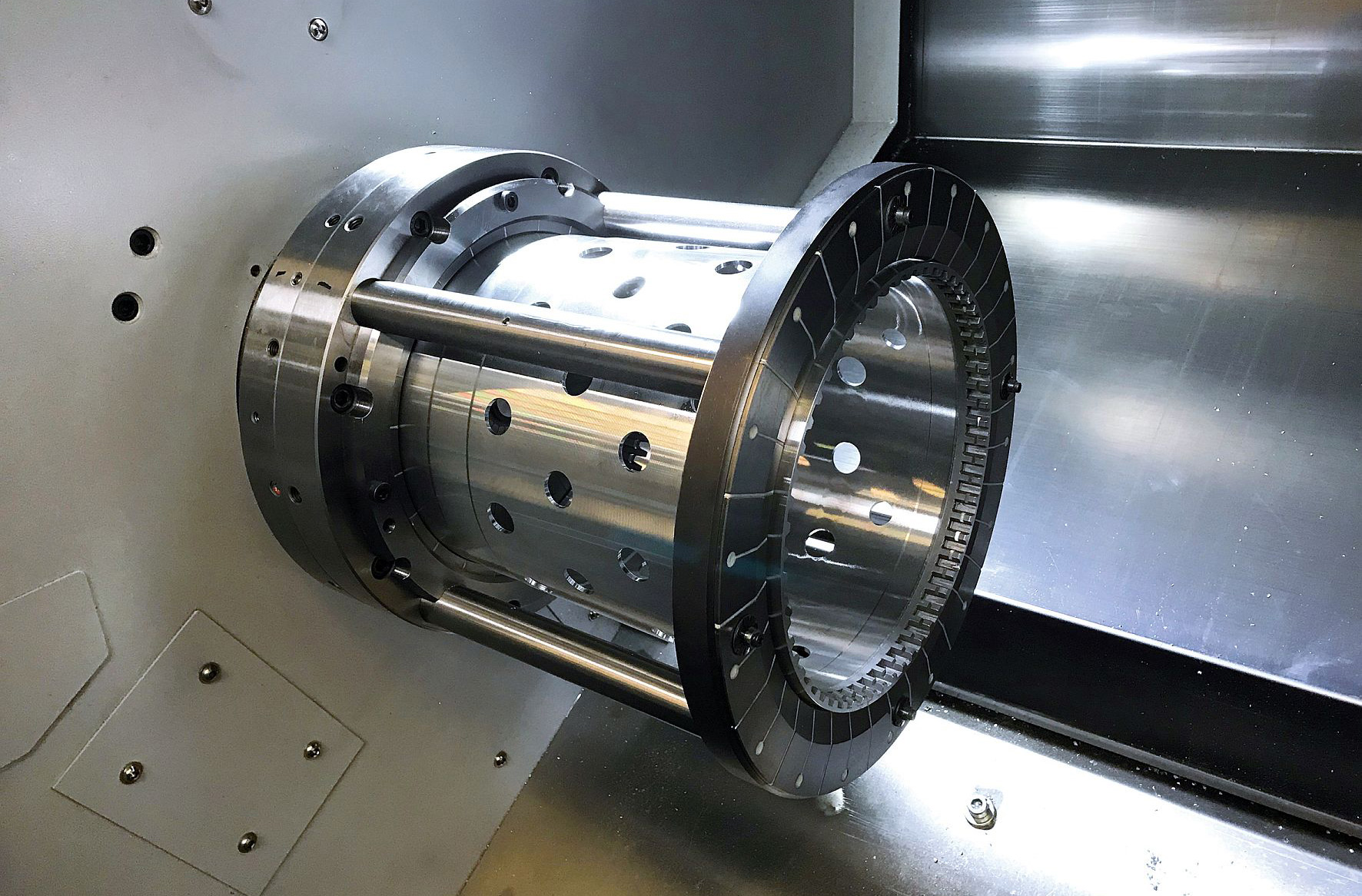
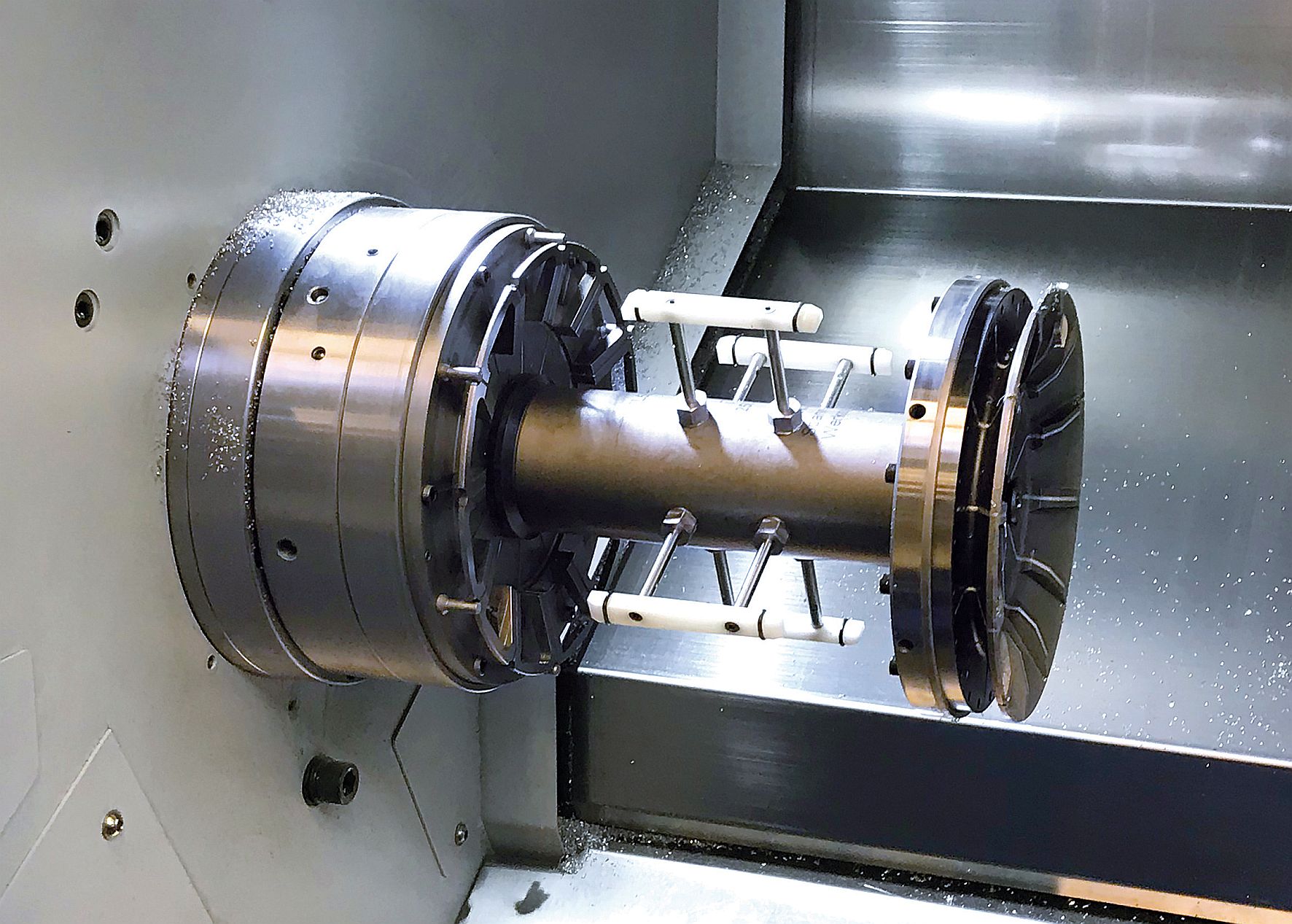
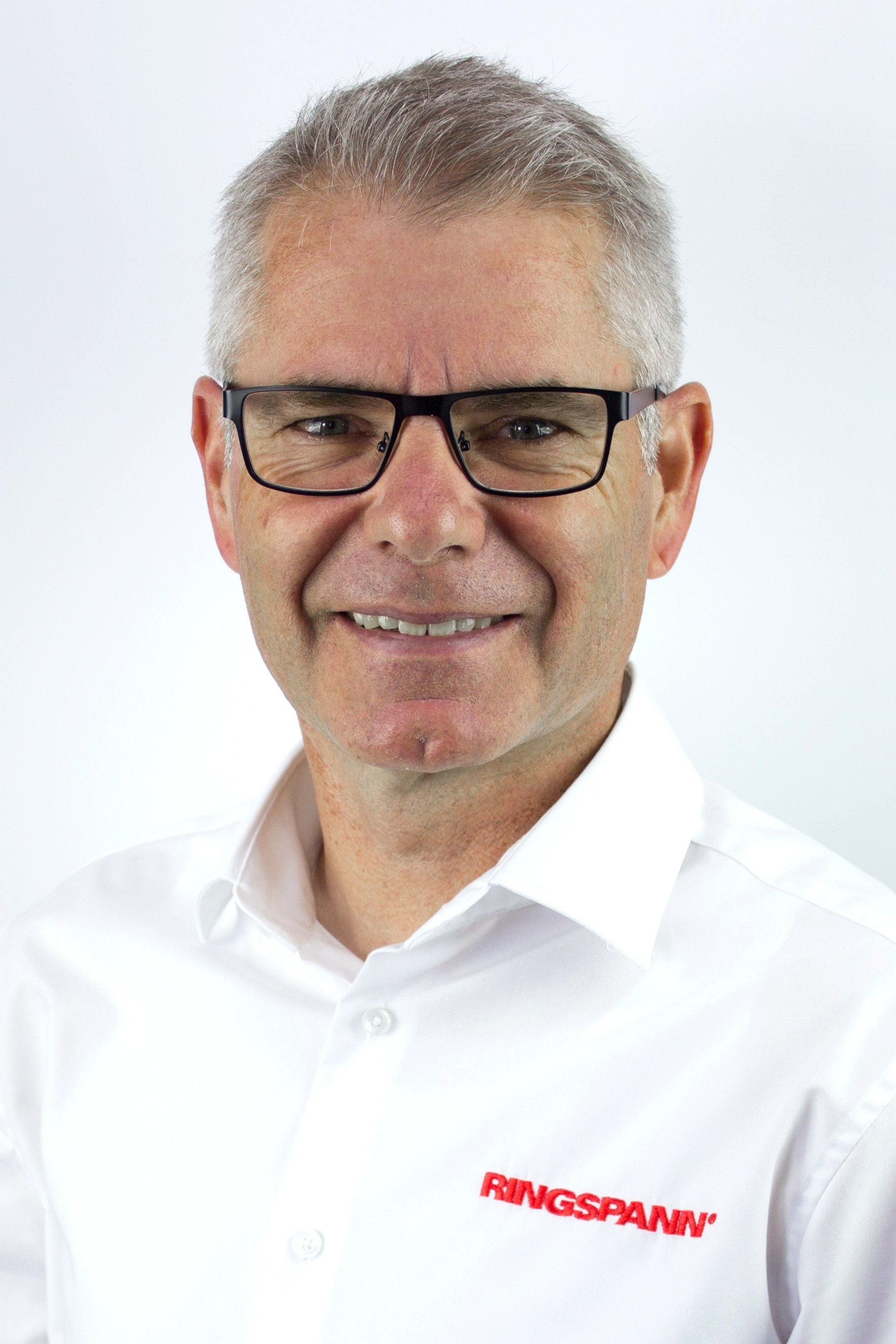
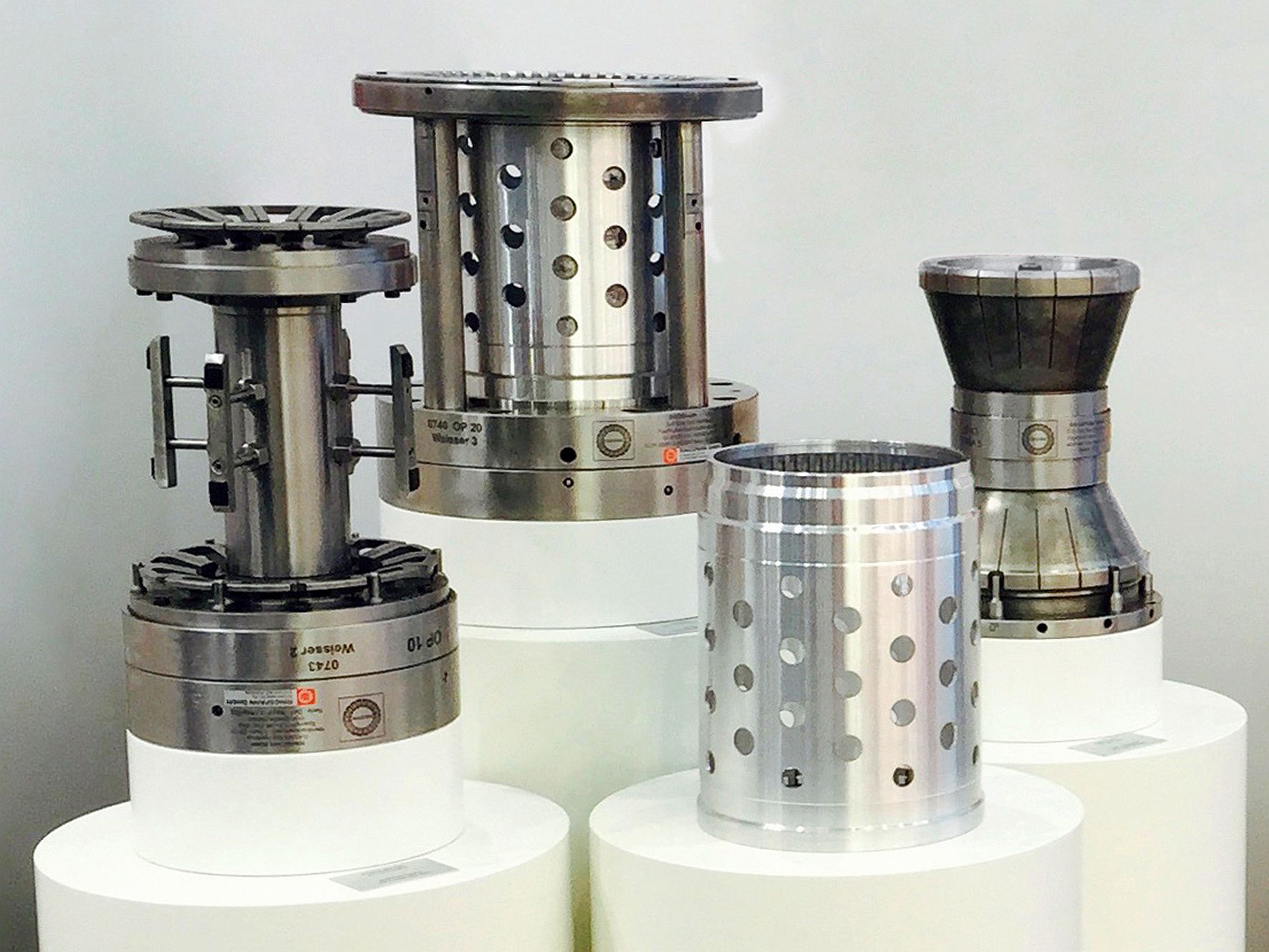
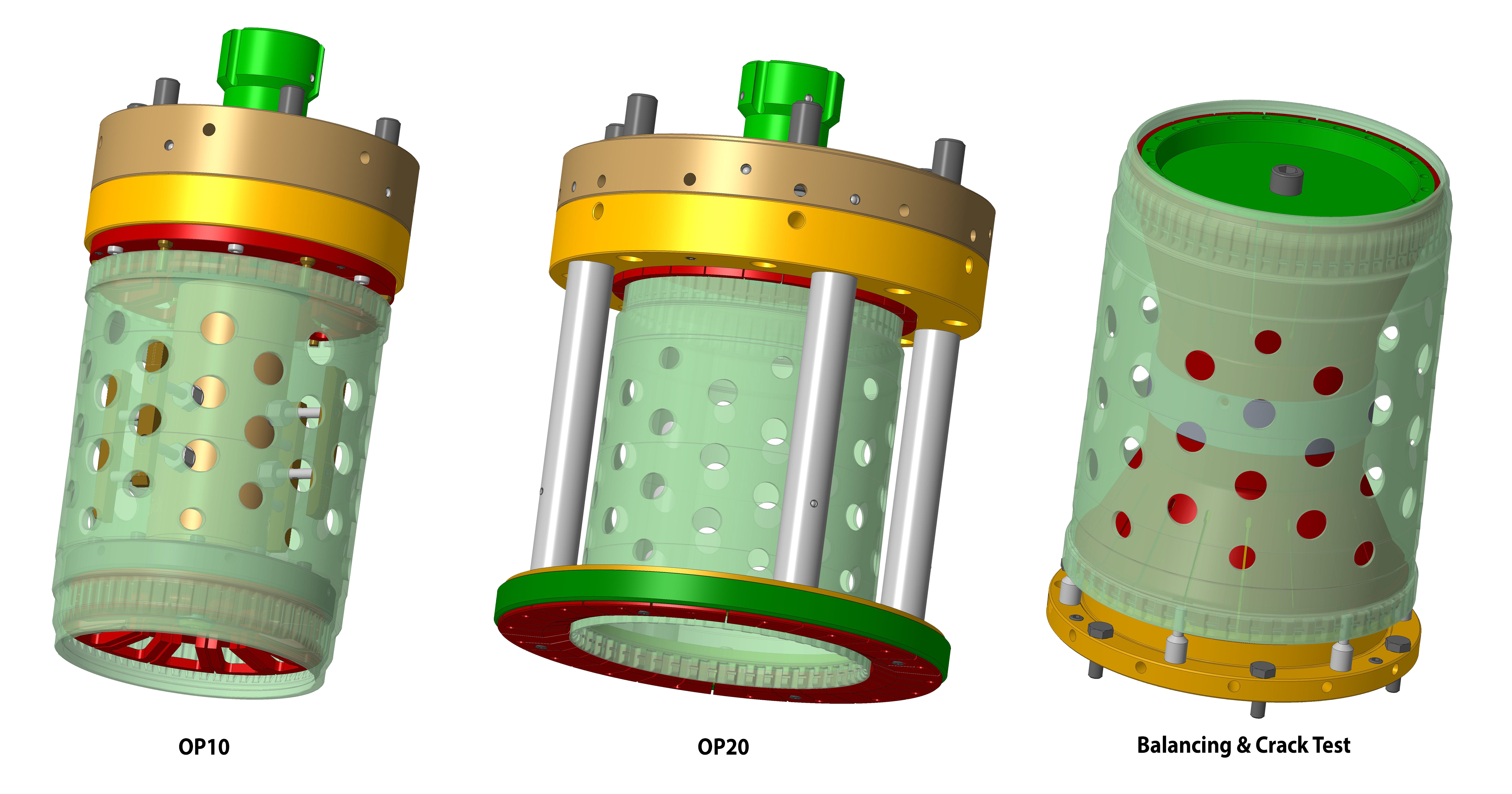